OCTC Announces 2023 Awards for Excellence in Environmental, Health, Safety & Security Performance
Ohio Chemistry Technology Council (OCTC) is proud to announce this year's Awards for Excellence! We are honored to recognize exceptional performances in environmental, health, safety and security by companies in Ohio’s chemical industry!
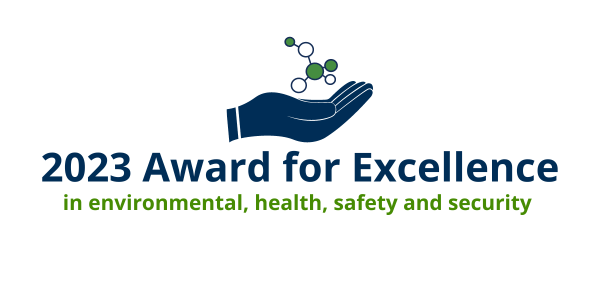
Eagle Award Winner
Nutrien Lima Nitrogen – Lima, Ohio
Award for Excellence Winners
In addition to demonstrating commitment and achievement in protecting people and the environment, a nomination must focus on a program or activity the company believes represents excellence in environmental, health, safety or security performance. Click on each site to read a brief description of their achievements!
The Ashland-Atlas St., Columbus, OH facility has made a commitment to find potential hazards throughout the facility and make improvements to abate those hazards. The leadership at the Ashland-Atlas St., Columbus, OH facility took a
proactive approach to potential employee safety issues. Historically, bulk bags of raw material were lifted into position with an overhead hoist. Once in position the operator would untie the bottom chute of the bag and guide it into the reactor. This practice put operator’s hands in a vulnerable position between a 500 kg load and the reactor. Thus, leaving operators hands and arms susceptible to crushing from a potential hoist failure. A project to mitigate this risk was brainstormed, agreed upon and engineered. A structure was built around the reactor that acts as a cradle and platform for the bulk bags which eliminates the risk to the operator’s hands and arms. Thanks to efforts like this our facility has now been injury free for over three years.
The Whitehouse Site had been having issues with water intrusion along the north wall of the Laboratory Building. The site was concerned about the Health and Safety of employees due to the potential for mold growth, the potential for electrical shock associated with electrical receptacle and power strips feeding workstations along the interior of the north wall getting wet,and the potential for slips and falls due to pooling water along the interior of the wall. An engineering review determined that there was an issue with the masonry block along the north wall. The project required approximately one thousand field hours for exterior masonry repairs and interior drywall
repairs. The project cost approximately $132,000 to complete needed repairs.
In 2021, Cenovus Lima Refinery was at 0.42 recordable injury rate; just below the refining OSHA recordable injury rate of 0.5. In 2022, Cenovus Lima Refinery set a priority for a recordable injury rate of 0.22 and ended the year with a recordable injury rate of 0.10, a record for the site and world-class performance. The site achieved this by being intentional in their discussion of occupational safety and personal accountability, improved field visits, and opportunities for employees to address root causes of occupational safety hazards.
The DuPont Dayton Site manufactures electronic grade polymers for use in the semiconductor industry. The site recently installed and commissioned numerous interlocks improving the safety of multiple high hazard manufacturing processes. These upgrades were identified during a cyclical Process Hazards Analysis (PHA) review conducted by a multi-disciplinary team consisting of operators, engineers, line leaders, and maintenance representatives. The additional interlocks act as an extra safeguard against overfilling vessels with flammable materials and were added to over ten individual process vessels. Each interlock provides an additional layer of protection to the operation, making the processes inherently safer.
DuPont’s West Alexandria site continuously looks for opportunities to reduce its environmental footprint. In 2022, a new process was put in place to eliminate the aerosol can hazardous waste stream. Used cans are punctured and residual solvent is collected. The solvent is disposed in an existing waste stream and the cans are then recyclable. This saves money by eliminating a hazardous waste stream. This shows how environmental improvements are compatible with business objectives and can be incorporated into everyday work processes.
In 2022 Emery completed a complete shutdown of the electrical grid for the first time in 40 years. The main station and 30 substations were inspected/overhauled and over 50 steam/condensate projects completed. Challenges to these projects included: over 200 contractors onsite, around the clock work, maintaining fire systems, alternative emergency communications/parking and security procedures. The entire project spanning 10 days was completed successfully and with no injuries or incidents.
Epsilyte LLC began 2022 with several recordable injuries and determined to take progressive steps to eliminate injuries at its newly acquired site. SafeStartNOW® was chosen for this purpose and involves 4 modules with 2 hours of classroom training for each module. After each module, there is 1 month period where the employees can put their learnings into practice. All employees have completed 2 modules and the site has not had an injury in 8 straight months. SafeStartNOW® crosses the boundaries of site safety and is a program used to strengthen family safety as well including a take home portion for the teen-age and younger children to encourage them to start the journey to a safe and healthy lifestyle. Epsilyte knows safety starts at home and is brought to work every day and is partnering with their employees to maintain a zero-injury workplace.
GFS Chemicals partnered with SafetySkills, a web-based learning management platform for organizing and administering training across the organization. In addition, the EHS&S and QA team has expanded the GFS Learning Management System profile with GFS Chemical's own training topics configured to each department, ensuring all areas receive the right safety and quality related training.
INEOS is committed to a Culture of Prevention to avoid injuries and ensure all onsite employees return home safely. In the spirit of the INEOS focus on “one job, one day, one week, one year at a time”, the facility sought to improve their safety plan in the areas of SHE training and process safety management. As of year end 2022 INEOS achieved its goal of three years in a row without an OSHA Recordable injury of an employee or contractor. This equates to nearly 1.5 millions injury-free hours.
The Lubrizol Corporation recognizes how critical it is for people working at their facilities to be provided an environment of safe and secure operations. The age of the Painesville plant and design of their systems results in the need to frequently perform operations and maintenance activities from elevated work surfaces. A comprehensive, multi-year plan was developed to identify, assess, and mitigate fall hazards throughout the site. Over 3 million dollars has been spent on this initiative. In the past two years alone, 20 Capital Projects and over 50 smaller improvements have been executed to reduce risks while working from heights.
As part of the safety journey of continual improvement toward Zero Harm, the Kraton Belpre site has developed and implemented a Critical Thinking program for all site employees and contractors. Critical thinking is integrated in the employee training and the on-going safety processes. Contractor orientation is inclusive of the same Critical Thinking elements. Stop Points are a key component of the Critical Thinking process, and can be called by any person working at the site, regardless of rank. Stop Points are evaluated, reviewed, and discussed as part of training, operations, maintenance, and capital projects. To be successful in safety, every person on the Kraton Belpre site is encouraged to be a positive safety contributor and engage the Critical Thinking process for every task, every day, and be empowered to stop the work to assure all safety principles are being met.
In 2022, McGean installed display tv's in both of their main production areas and maintenance shop. These tv's have a rolling slideshow of different safety items they feel are needed to be seen daily. The slides are changed on
a frequent basis based on different hot topics that come up in a safety chat, safety training, or safety committee meeting and also used to update employees regarding contractors that are on site. The main goal of the tv is to show that McGean cares about employee safety.
The PPG Barberton plant developed a comprehensive Continuous Improvement Framework for the OLED department which targets efficiency improvements and waste reduction, but the main emphasis is safety. This framework includes daily Gemba walks with department leadership and weekly safety walks with operators on each shift that focuses on hazard identification and elimination. A database is utilized to capture opportunities and ensure development and implementation of corrective actions.
PPG - Barberton, Ohio
The PPG-Barberton Fire Risk Minimization Program is designed to reduce the likelihood and magnitude of potential fire incidents at the facility, primarily focusing on the activities in the Teslin plant. The Fire Minimization Team is a cross-functional group comprised of engineers, EH&S professionals and P&M employees, meet regularly to identify gaps and drive risk reduction projects to completion. Through their efforts, the site has achieved a 40% reduction of fire-related incidents in Teslin.
The PPG Cleveland plant includes a pedestrian pathway that runs from the north to the south end of the plant. Employees recognized one area on this pathway had increased risk for interactions between fork trucks and pedestrians. The facility installed a stationary motion sensor and alarm system that would detect fork truck traffic approaching the pedestrian pathway. This system provides audio and visual alarms to pedestrians traveling on the pathway when a fork truck is in motion nearby.
The PPG Delaware facility is continuously repairing and replacing concrete around the facility due to normal wear and tear. Previously, construction debris had been sent to a landfill 40 miles away. The nearby limestone quarry was in search of clean hard fill for areas of their property that were no longer mined. The quarry is less than 5 miles from the facility. The facility environmental department completed an audit of the quarry to determine if it could be an approved disposal/recycling location and was approved by PPG corporate. The facility was able to recycle 1470 tons of construction debris and save $116,000 in disposal/transportation cost in 2022. Due to this approval future planned construction projects will benefit from the new recycling option. The site won an internal environmental impact award for PPG. The application will explain further the sustainability impact of reduction in waste, energy and other savings.
PPG Euclid has a manufacturing workcell that is dedicated to making Zirconium technology products. This area has a dedicated waste stream due to the nature of the products. Most of the products take the same raw materials. Prior to the project implementation rinse water from the work cell was being shipped to a waste disposal company. Recycling this rinse water will save $26,900 in cost avoidance in hazardous waste disposal and eliminate 34,500 lbs of hazardous waste generation.
In 2022, Solvay Cincinnati implemented a Planning Wheel as an effort to minimize the amount of product changes throughout the year. Each product change utilizes 113,000 gallons of water and produces 6 Tons of material into landfill. Through the implementation of a planning wheel, they were able to reduce this by 77%. This equates to 1.3 millions gallons saved and 73 fewer tons of material in landfill. Solvay Cincinnati is committed and on track to further reduce these wastes through other initiatives in the facility.
Solvay – Cincinnati, Ohio
Solvay Cincinnati uses a technique called ICP-MS (Inductively coupled plasma mass spectrometry) in the analytical laboratory for measuring elements at trace levels. This technique is used daily to release finished products to customers. To prepare for this measurement tool, the finished product must be in liquid form. Since Solvay’s product is an alumina powder, they have to digest this with a variety of acids. This poses a safety concern to the lab analyst who uses these chemicals daily. With the introduction of a microwave digestion unit, the Solvay Cincinnati team was able to eliminate the use of most acids to perform this analytical measurement. This change improved safety and storage of hazardous chemicals.
Solvay – Cincinnati, Ohio
The Solvay Cincinnati site achieved another year without an OSHA recordable injury for calendar year 2022. This completes the third year with no recordables. The Cincinnati team with the facilitation of the HSE Manager has consistently reviewed and updated the Site Safety Program to achieve this significant milestone. In 2022 the Site Safety Committee was reformatted and their focus on Safety & Environmental Engagement and identifying Near Misses with corrective actions led them to this continuing success. They ensure the entire team focuses on identifying hazards, reporting the situation, and taking action with a sense of urgency and use tools such as Behavior Based Safety reporting, Safe moments before meetings, Safety tips in their newsletter, and sharing Safety lessons learned across the plant and the company.
Solvay – Cincinnati, Ohio
70 tons of Alumina, a powder utilized in coating catalytic converters for automotive emissions, was found to be out of specification for some customers. The material was high in moisture content (50 tons) and rare earth elements (20 tons). To recover this material and prevent landfill, Solvay Cincinnati recommissioned equipment used to recover material from super sacks into bulk storage silo. About 30 tons of material were recovered into a silo and re-processed within specification products to release to customers. About 20 tons of material were recovered, mixed and milled to be sold as a different product. The remaining material was recovered and dried to reduce the moisture content and sold to customers. The recommissioning of this equipment and Solvay's efforts for the environment prevented 70 tons from being landfilled and that much more from having to be re-produced from raw material.
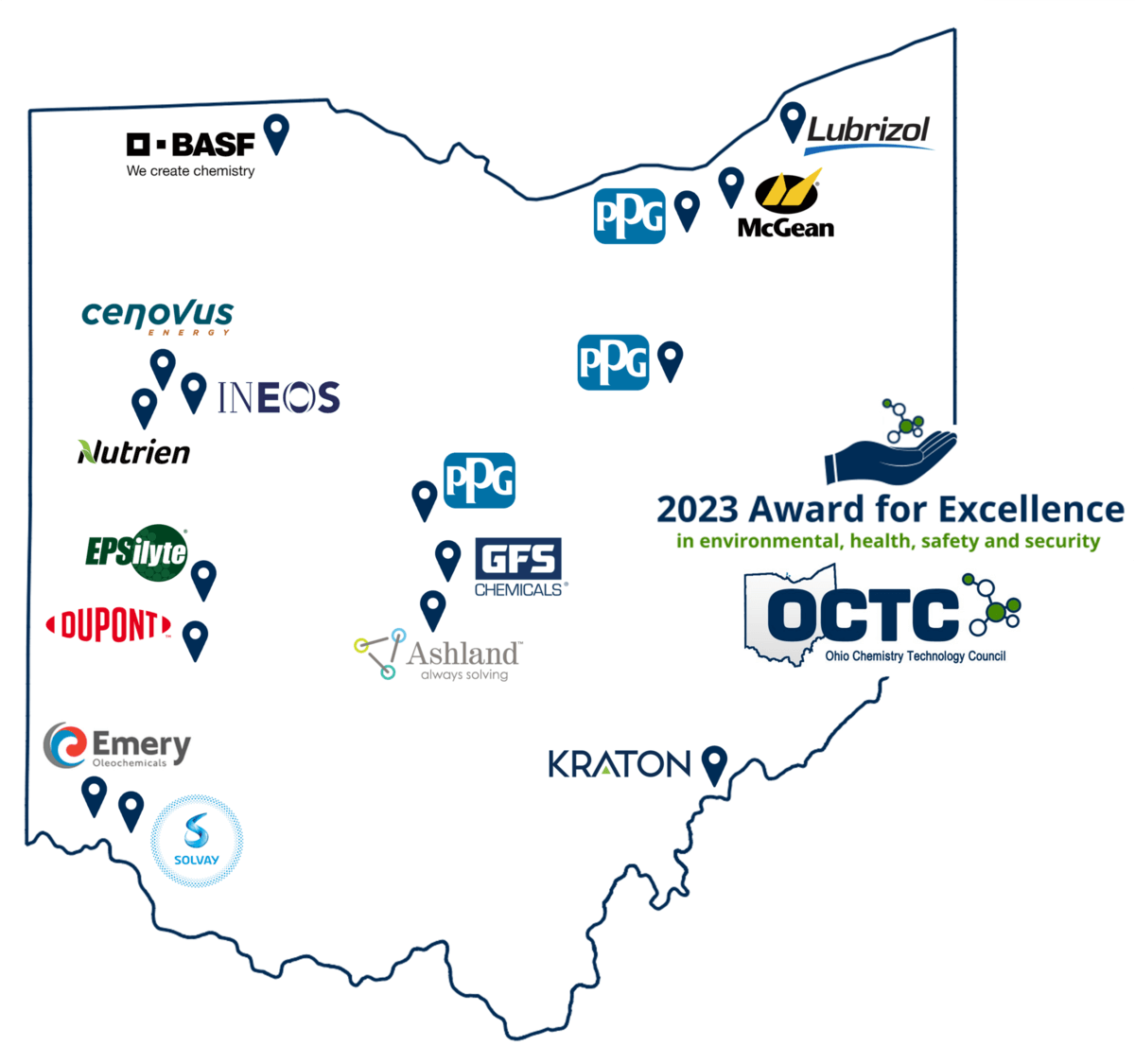