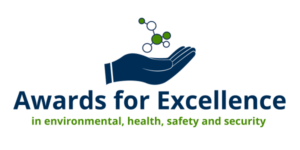
Each year, exceptional performances in environmental, health, safety and security by companies in Ohio’s chemical industry are recognized by the OCTC through the council’s Awards for Excellence. These companies have demonstrated dedication to a method of continuous improvement that keeps our communities and state a safer and healthier place to live and work.
2024 Awards for Excellence Winners
Ohio Chemistry Technology Council (OCTC) is proud to announce this year's Awards for Excellence! We are honored to recognize exceptional performances in environmental, health, safety and security by companies in Ohio’s chemical industry.
Eagle Award Winner
OCTC is excited to announce this year's Eagle Award for Excellence in Environmental, Health, Safety & Security Performance. Our panel of judges selected this program for standing out in scope, implementation, impact and sustainability.
McGean – Cleveland, Ohio
In 2023, McGean started to evaluate manual processes for improvements. One such process is charging a hazardous chemical to a reactor for batch processing. The chemical in question is hazardous to human health and was being charged to the reactor manually. McGean took an in-depth look at this process for safety and performance improvements. Once the reviews were conducted, equipment was purchased and installed. The charging of this hazardous chemical is now fully automated. An operator used to have to don a significant amount of PPE, and manually hook up the hazardous cylinders to charge lines. Now the operator controls the process from a computer screen. This not alone protects the operator but allows the operators to have much more control over the hazardous charge. The automated process was installed with many engineering controls, data acquisition points, and interlocks. If something does go wrong, an operator can now fix the issue with a computer screen instead of manually fixing the problem up close and personal.
Award for Excellence Winners
This year, 20 member companies have been selected to receive an award for excellence in Environmental, Health, Safety or Security Performance. Each facility of a member company submitted a nomination on its own behalf which was then submitted and reviewed by our distinguished panel of judges.
In addition to demonstrating commitment and achievement in protecting people and the environment, a nomination must focus on a program or activity the company believes represents excellence in environmental, health, safety or security performance. Click on each site to read a brief description of their achievements!
The BASF Elyria team conducted an active shooter tabletop drill to help the site be better prepared in case of an emergency in which police involvement would be required. City of Elyria Chief of Police and an experienced Lieutenant participated alongside the site’s leadership team, BASF Corporate Security, and security contractor. The drill resulted in several actions taken to better prepare the site and Elyria Police to respond to an event. The site also gained valuable insights from the perspective of the Elyria Police Department to better allow them to succeed in case something occurs at the facility.
BASF Whitehouse had issues with water flow to Application Training Center safety showers and eye wash stations over the years due to significant fouling (build-up) in the water loop - periodically restricting flow. In addition, the facility safety showers and eye wash stations did not consistently meet the OSHA water temperature guidelines. Because of the flow issues and seasonal water temperature variation, the facility installed a new tempered water loop system. The ATC tempered water loop system is comprised of an indirect hot water heater, tempering valve, circulating pump, and copper piping connected to seven eye wash stations and safety showers. The project was estimated to cost $80,000 but due to the support and efforts of site engineering and maintenance, the total project expense was $74,741.
Lighting is inherently important for security and occupational safety at Cenovus Lima Refinery’s 450-acre facility and 24/7 operation. However, larger more urgent electrical repair work continued to take priority. In 2022, the refinery’s Joint Health and Safety Committee took up the issue to make sure process operators’ concerns were heard and maintenance technicians had what they needed to make replacements. In 2023, a project was developed to replace hundreds of fixtures. To date, about 700 outdoor light fixtures have been replaced and a new annual program for lighting surveys and repairs will be used going forward. Sixty new street lights (along with associated junction boxes, mounting arms and hardware) are expected to be installed by the end of Q1 2024.
The Chemtrade Cairo facility recently celebrated 6 years injury free. The key to this achievement is ensuring everyone knows and can safely exercise their right to stop work at any time. Additionally, the facility annually develops a site Safety Plan that focuses on improvements to employee engagement, operating discipline, and site conditions. In 2023, despite achieving 5 injury free years, the facility added the DuPont STOP program to its toolkit to further improve performance.
Chemtrade’s Toledo Water facility manufactures water treatment chemicals used by private businesses and public municipalities. In 2019, the site implemented a program to divert 100% of the solid wastes generated by the process from the landfill. Since 2019, over 10 million pounds of this material has been beneficially reused as an ingredient to make cement preventing the material from ending up in a landfill.
Epsilyte’s dedication to innovation and sustainability drives their mission to revolutionize EPS recycling while partnering with major corporations to advance responsible waste management practices. Their commitment to sustainable practices is evident through significant investments in recycling technologies. Their innovation efforts led to the successful development and commercialization of their pioneering recycled content product marking a significant step in offering sustainable products. In addition, Epsilyte sourced 1.08MM in 2022 and 1.375MM in 2023.
GFS Chemicals utilizes three separate Business Units to focus on different product markets. Their EHS team has the responsibility of leading projects that are targeted to reducing their environmental footprint and improving sustainability. In 2023, the team was tasked with implementing a project to reduce the city/well water consumption and sewer output. To accomplish this goal, they performed a facility shutdown in conjunction with an in-depth process analysis for water consumption. This resulted in the identification of several opportunities for improvement in their manufacturing processes which included upgraded valve systems, continuous flow limitations on scrubber tanks, implementation of proactive maintenance checks on reactor condensers, and the upgrade of automation monitoring equipment. The implemented changes resulted in a significant reduction of over 60% water usage in 2023 when compared to the previous three-year average (2020-2022).
Heritage Thermal Services promotes safety by way of two formal programs: Target Zero and 6Safety. The facility also conforms to OHSAS 18001 for oc- cupational health and safety. In 2023, the company achieved a million-worker hours without a lost-time accident for the period from Oct. 6, 2020 to May 31. The National Safety Council recognized the faciity for this achievement.
INEOS has the vision of becoming the first Green-Listed site within the Nitriles division. In 2023, they improved their safety plan in the areas of Internal Motivation, Organizational Commitment, SHE training of all employees and PSM. INEOS achieved its goal of four years in a row without an OSHA Recordable injury of an employee or contractor. This equates to nearly 1.8 million injury-free hours. For employees only, they achieved their seventh year in a row without an OSHA Recordable.
Kraton identified an opportunity for HSES presence at all hours of continuous operation across the facility. To provide this coverage, Kraton developed a course designed to provide a select group of technicians the opportunity to develop skills necessary to safely perform the duties of an HSES representative, referred to as a “Red Hat”. The positive influence of the Red Hats drives safety culture by consistently demonstrating commitment to continuous improvement.
The Lubrizol Corporation Painesville facility is focused on continually improving the Health, Safety, Compliance, and Productivity of their facilities. With higher expectations for housekeeping, hazard recognition and mitigation, efficiency, and environmental compliance, the facility implemented a structured 5S program to drive the culture change needed to meet these expectations. The facility deployed 5S into 41 of its 107 different zones in an employee led, leadership supported effort.
In 2023, The Lubrizol Corporation achieved zero recordables and zero lost time injuries at the Wickliffe corporate headquarters. The site achieved zero Tier 1 and zero Tier 2 process safety incidents as well as zero contractor injuries. Achieving zero recordables is an exceptional first-time milestone given the complexity of operations at the site. In 2023, the Wickliffe site also achieved recertification of VPP Star; the fourth time for the site since attaining VPP Star status in 2007.
In 2023, McGean started to evaluate manual processes for improvements. One such process is charging a hazardous chemical to a reactor for batch processing. The chemical in question is hazardous to human health and was being charged to the reactor manually. McGean took an in-depth look at this process for safety and performance improvements. Once the reviews were conducted, equipment was purchased and installed. The charging of this hazardous chemical is now fully automated. An operator used to have to don a significant amount of PPE, and manually hook up the hazardous cylinders to charge lines. Now the operator controls the process from a computer screen. This not alone protects the operator but allows the operators to have much more control over the hazardous charge. The automated process was installed with many engineering controls, data acquisition points, and interlocks. If something does go wrong, an operator can now fix the issue with a computer screen instead of manually fixing the problem up close and personal.
At Nutrien Lima Nitrogen, emergency help buttons were installed to alert personnel that a lone worker is in need of urgent assistance. Around 60% of plant personnel operate out of the central control area. The central control area is always occupied, with a requirement for a minimum amount of personnel to control the process and manage alarms. Because 5 of the process units are far away from the central control area, 40% of plant personnel are often working alone. During medical emergencies, a lone worker may not always have the ability to use the phone or radio to alert personnel of a rapidly escalating situation. In reaction to this risk, we installed emergency help buttons to alert personnel that a lone worker is in need of urgent assistance. When any of the buttons are pressed, an alarm will sound to the central control area, where resources can then be routed to the area in need.
PPG manages 600 acres of high-pH waste material in surface impoundments known as Lime Lakes. One impoundment has still bottoms from PPG’s manufacturing of chlorinated solvents placed (1949-1970s) before environmental laws. The state EPA would call this area the most contaminated site in Northeast Ohio. That all stopped in 2022 when PPG completed a 40-acre landfill type cap. The cap ensures contamination is not moving offsite, is protective of human health, the environment and PPG’s reputation.
The PPG Barberton Gemba Walk Program is designed to identify risks and hazards throughout the facility. Gemba walks emphasize on the continuous improvement of safety. Each week, employees meet to discuss and walk through departments across the plant. After the walk is complete and hazards or risks are identified, they are discussed in the group and action plans are created. Each department is held accountable for hazards and works to correct them to promote safety throughout the site.
During the 2023 calendar year, an OLED Department employee experienced an OSHA recordable when they tried to open a valve that had become difficult to maneuver. As a result, The OLED Department made an entry in their Oper- ational Excellence Database, Abnormal Conditions section, for hard-to-open valves. Operators, who came across difficult to open valves, would make an entry in SharePoint. The list was then used to place work order for valve re- placement and repair.
The PPG Cleveland facility installed an overfill protection system for paint dispense. The overfill system significantly mitigates the risk associated with spills by no longer having to rely on visually measuring the liquid levels from a ladder. The new system utilizes both pressure differential and high level contact probes to maintain appropriate liquid levels. The devices are tied into visual & audible alarms indicated on an HMI. Upon activation of the HL, the feeding pumps are shut down.
The PPG Cleveland facility relied on its leaders to identify and mitigate risks for many years. The EHS team launched a GEMBA process to help change this culture and drive risk recognition and abatement across all levels of the organization. The GEMBA process meets for 1 hour weekly, includes 50-60 participants, and has proactively fixed hundreds of hazards in the facility. It has also increased PPG employees’ ability to recognize and abate risks and knowledge of when to ask for help.
PPG Lima Coatings Services was able to eliminate a hazardous waste stream by switching from a disposable 55 gallon resin bead drum filter to a reusable filtration system. By switching to a reusable filtration system they have eliminated all waste drums, reduced the cost of purchasing filter drums vs installing and maintaining the renewable system, saved the cost of training in order to meet large quantity generator training requirements, and reduced the frequency of planned inspections from the EPA.
A batch process that generates an explosive gas by-product routinely exceeded the safe operating limit (SOL) for gas concentration. A PHA was performed and determined that the risk of poorly controlled concentration was too high. The team recommended converting the process to semi-batch to control the gas concentration to a safe setpoint. Since implementation, this change has been successful at controlling the gas concentration within the SOL and allowing for safe shutdown at any time.
At the Solvay plant, filtration using fresh RO water was essential, yet it also incurred significant costs. To align with Solvay’s sustainability goals, the site aimed to reduce fresh water intake. They focused on optimizing the amount of fresh RO water used in the filtration process for SRL. The target was to decrease fresh RO water usage while maintaining consistent contaminant levels. This effort not only saved on variable costs but also contributed to Solvay’s larger goal of reducing fresh water intake. By making this change, the site anticipated saving approximately 5,216,400 gallons of water per year, resulting in significant cost savings.
Solvay Cincinnati rescued 150 tons of silica, avoiding landfill and potential layoffs through innovative collaboration with Solvay Chicago Heights. This project addressed a critical issue involving the recovery of 150 tons of silica, which was quarantined in three railcars due to the presence of metallic fragments. Without intervention, this material would have ended up in a landfill, posing environmental concerns. This initiative not only solved an environmental issue but also helped Solvay Cincinnati by providing additional activity for the site, thereby avoiding potential layoffs. It generated approximately $25,000 in profits for Solvay Cincinnati and provided equipment worth $30,000 for future projects. For Solvay Chicago Heights, it unblocked around $150,000 of working capital and resulted in the sale of silica as prime grade, with an additional cost of $20,000 for packaging and logistics compared to landfilling.
Solvay Cincinnati avoided landfilling Boehmite Alumina by repurposing upgraded railcar equipment, securing a buyer-turned-client for 80 tons of material. This sale yielded a contribution margin and spurred further orders for prime grade material.
Team Synthomer at Akron operations lives the motto, We Always Have Time to Work Safely. 3000 days and counting, there were zero OSHA recordable injuries and zero Tier 1 or Tier 2 Process Safety events in 2023. Using continuous feedback, permit to work systems, live auditing, and implementing best practices from industry, and Synthomer sites globally, the Akron site embraces the company’s 10 SHE Principles and 10 Golden Rules making it a Synthomer SHE site of excellence.
Being Serious About Safety is a core value for Univar Solutions. They are an organization that respects and follows the applicable safety laws and regulations, work towards adhering to the highest industry standards and work with industry associations to develop new standards intended to benefit every stakeholder in the chemical and ingredient distribution supply chain, motivate continual improvement from our people through safety initiatives, and provide trainings delivered to all our teams on the topics most relevant to their roles through a combination of in-person training, online materials and safety-focused events across the business. With a targeted capital investment in facilities and fleet to continually improve safe working conditions and maintenance investments to ensure safe and uninterrupted operations. Univar is a leader in procedures for the safe storage, blending, packaging and transportation of products, incident reporting, investigation and root cause analysis to prevent reoccurrence.